Post-WWII – The First Commercial Jet Airliner
JET ENGINE DEVELOPMENT
The Jet Engine was developed independently by Frank Whittle from the British Royal Airforce and Hans von Ohain a German Physicist with Heinkel. Ohain was the first to Flight Test a Jet engined aircraft, the Heinkel HE 178 in August 1939. Development was slow and the German Messerschmitt 262 Jet Fighter came into service with the Luftwaffe shortly before the end of World War II in 1945 See: 5. Prisoner of War Camp, Nuremberg The British Gloster Meteor Jet Fighter was also involved at the end of the war.
COMMERCIAL JET AIRLINER
Jet engines had only been used in military aircraft as they were expensive, only the military could afford them. The airliners in service mainly the Lockheed Constellation, Douglas DC4/6 and Canadian North Star all had Piston Engines and propellors.
The DeHavilland Aircraft Company of England decided to produce a Jet Engine powered airliner and named it the COMET 1. Officially it was the DH106. I think they had done some work on it slightly before the end of the War. It first flew on 27 July 1949 and went into service with BOAC (British Overseas Airways Corporation) on 2 May 1952.
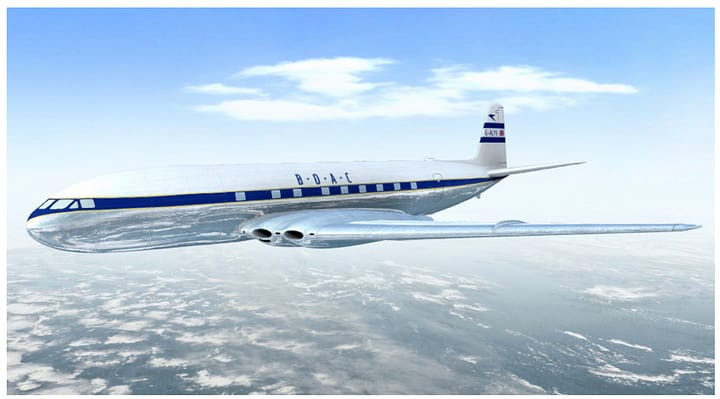
As can be seen by the picture, it looked very much like the present jet airliners with the exception that the engines were mounted in the wing root, 2 each side. Jet aircraft of today mount the engines usually under the wings singularly and not together. The Comet Engine location makes the wing structure complicated and as the wings contain fuel it reduces the amount of fuel that can be carried in the wing. Also, should an engine have a failure it may damage the other engine beside it. The engines used were the DeHavilland Ghost 50. The cruising speed of 460 miles per hour and altitude of 35,000 feet were slightly less than today’s jet airliners but much ahead of the piston-engine airliners. As you will notice the aircraft had square windows and due to the higher altitude, the fuselage pressure was twice as high as the piston-engine airliners.
SERVICE
The Comet went into service on 2 May 1952 with BOAC and was very popular. Its’ passengers got there faster, and the high altitude was mostly above the weather so it was a much smoother ride. There were 6 crew and 36 to 44 passengers. They took the Queen for a flight in the Comet and people were visiting all the airports it was scheduled to land at. It was considered a British national icon.
However, there were problems:
1. On 26 October 1952, an aircraft ran off the end of the runway during take-off from Rome Italy. The aircraft was damaged, but no one was injured. This was considered to be pilot error.
2. On 13 March 1953, the aircraft crashed soon after take-off from Karachi. It was a similar accident to the above but this time it hit a stone bridge and the aircraft caught fire. All 11 occupants were killed. In June 1953, another similar accident occurred in Dakar Senegal but there were no injuries.
3. On 2 May 1953, the aircraft took off from Calcutta, lost radio contact and was seen coming down in a blaze of fire through a severe thunderstorm and crashed into the ground. The aircraft was considered to have been broken up by the thunderstorm. As a result of this accident and previous accidents, flight instructions were issued to pilots, modifications were made to the wing, and future aircraft were fitted with weather radar.
4. On 10 January 1954 aircraft licensed G-ALYP (“Yoke Peter”) disintegrated in flight soon after taking off from Rome. All aircraft were grounded They did not know what happened and decided to strengthen the aircraft and made 50 modifications to the aircraft and let all the aircraft go back into service.
5. On 8 April 1954 another aircraft G-ALYY (Yoke Yoke) disintegrated after taking off from Italy and all aircraft were grounded. After this, they concentrated on finding the cause of these last two accidents. A large investigation board was formed under the direction of the Royal Aircraft Establishment. The British Admiralty had started a salvage operation raising the remains of Yoke Peter. It was a very difficult job in 500 feet of seawater and assembling the remains on land. Prime Minister Winston Churchill intervened and said that it would be worth the cost to solve the mystery.
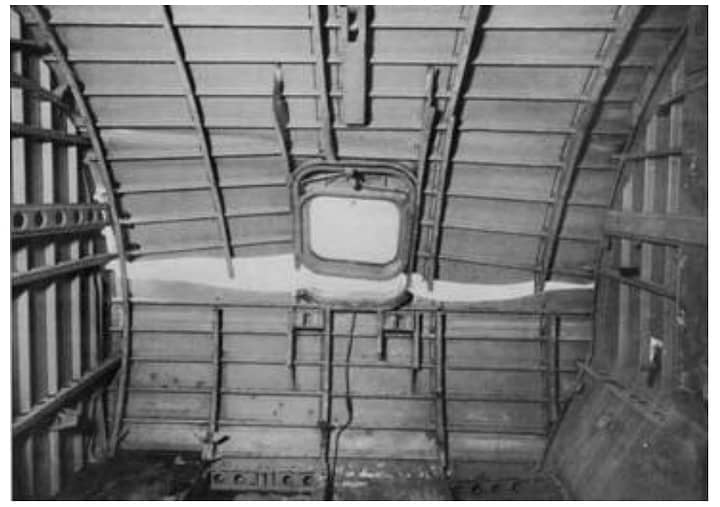
FATIGUE
Fatigue is caused by many variations in stress which then causes cracks in the metal. It’s like the metal wears out. There are stress variations in the fuselage due to stresses in flight caused by pressurization which varies with altitude and goes to zero on landing. This is called a cycle. Stresses concentrate in the structure where there are sharp changes such as at window corners.
They decided to carry out a fatigue test on G-ALYU and placed the aircraft in a tank and filled the fuselage with water to simulate the pressurization pressure in the fuselage. Water was used as it was virtually incompressible and would not cause an explosion like air would when the fuselage cracked. The water pressure was cycled from in-flight cabin pressure to ground pressure (a flight/cycle) every 3 minutes until a fuselage failure occurred. The fatigue life determined was 3057 cycles and the failure was at the forward escape window. Yoke Peter had 1290 flights and Yoke Yoke had 900 flights when they were lost.
Fatigue testing had been done by DeHavilland and came up with a life of 16,000 flights. Unfortunately, the fuselage they used for the fatigue test had already been used for a static proof test (no cycling involved) which caused plastic deformation in the fuselage. This improved the fatigue life of the fuselage and came out to be 16,000 flights. The effect of the plastic deformation was not known at the time. Even then they were not sure if it was fatigue on the aircraft and visited the remains of the crashed aircraft and found fatigue at the corners of the windows.
The Certificate of Airworthiness was revoked/cancelled and this was the end of the Comet 1.
DISCUSSION
Accident investigations are used to find out what has caused them (not for legal purposes) and whether there is a need to improve the safety situation This as a requirement was a safety situation and introduced Metal Fatigue to Aircraft Certification. Sadly, DeHavilland had lost their lead in the introduction of Commercial Jet Airliners but safety had to come first. Fatigue had become a safety requirement and had been introduced into the safety requirements as below.
FATIGUE AND FAIL-SAFE
The applicant could come up with a Fatigue Life beyond which the structure will need to be replaced or rebuilt. Alternatively, the structure could be designed that damage would not be critical for safety. The DHC Twin Otter Aircraft has a Fatigue life of 33,000 hours on the wings which must be changed or rebuilt. The DHC 8 has crack stoppers that will restrict the length of the crack so it does not become critical. Recently a Boeing 737 had a skin crack in flight and the aircraft lost pressure and came back and landed.
DAMAGE TOLERANCE
Damage Tolerance now replaced Fatigue and Fail-safe. Since fatigue is very well known today the design requirements have now come out with Damage Tolerance. By test or analysis or a combination of both, It can be accurately known when and where fatigue cracks will occur. Inspection methods are very good and are used to inspect these areas on a timely basis.
SIGNIFICANCE
The Comet 1 was ended and DH had to redesign the aircraft and went back into service in 1958 but had lost its early advantage. The Boeing 707 came into service and sold many more aircraft than the Comet.1. The B707 was designed under Fail-Safe Requirements. However, the Comet heightened the need for total attention to Fatigue for all aircraft after that, and following development knowledge on Fatigue thereby increasing aircraft safety greatly.
See the DH Comet 1 in flight and learn more about it: https://youtu.be/qNIS0M-vLgY
Author: Keith Walker P.Eng. (Ontario)
Mr. Walker is a retired Transport Canada, Aviation Dept. Engineer. If you have any questions about any type of aircraft or comments on the article please contact Mr. Walker at aviationcomet1@gmail.com